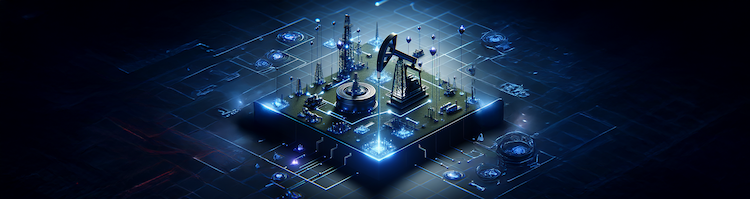
Integrating SCADA Systems with IoT and AI
Integrating SCADA systems with Industrial IoT and AI technologies is more than an upgrade—it is a revolution in oilfield operations. These technologies are transforming how oil and gas assets are monitored, managed, and maintained—unlocking new levels of safety, reliability, and efficiency. Explore our SCADA solutions to learn how your operations can benefit.
July 3, 2025
4 min